Push Back Rack | Stockton
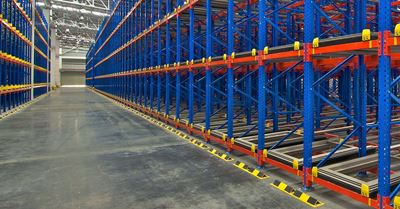
Raymond West offers pushback rack in a variety of styles and capacities.
We are one of the largest industrial racking suppliers in the state.
Call us today at (800) 675-2500
What Is Push Back Racking?
Push back racking (often called pushback rack) is a high density pallet storage system that allows pallets to be stored from 2 to 6 units deep. Pallets sit on nested shuttles that travel up a gentle slope as products are added, or “pushed back” from the front of the rack.
When products are later unloaded, the pallet adjacent to the foremost pallet slides back down the gradient to the facing position.
Push Back Rack Advantages And Disadvantages
Push back racking is ideal for some applications, but is not appropriate for every warehouse. There are several favorable and possibly unfavorable aspects to consider.
Higher Density Storage
Since push back pallet racks can store between 2-6 pallets in any given position, they can recover somewhere from 1-5 aisles, which represents a sizable chunk of warehouse space.
Less Forklift Travel
With a reduction in aisle number, lift trucks don’t have to rack up as many hours, reducing equipment wear and increasing efficiency. Reduced forklift traffic also makes a safer environment within the warehouse. Less travel directly correlates to fewer safety infractions.
Greater Selectivity
Push back rack offers a nearly perfect mixture of selectivity and storage efficiency. Different from drive-in rack, where full bays are generally only one SKU, pushback rack features direct access to a much greater number of pallet positions from the face.
LIFO Configuration
Unlike pallet flow rack, which is a First In First Out (FIFO) variety of system, push back rack is a Last In First Out (LIFO) style of plan. LIFO systems are not ideal for products with an expiration date, because goods that are stored first will often sit for long stretches of time as products are loaded and removed from the rack face.
How Does Push Back Racking Work?
A pushback rack system includes a couple of rails declining in the direction of the aisle and a set of interlinked shuttles which move on these tracks.
The first pallet is placed on the top cart by a forklift. When another pallet is positioned, the forklift operator nudges the primary pallet back and places the second pallet on the adjacent cart. The very last pallet placed in the lane is seated on the rails.
In the unloading process, carts loaded with pallets glide down the tracks. Lift truck drivers pull each pallet in succession until the lane is empty, or supplement additional pallets, refilling the lane.
Push Back Pallet Racking For Sale
To learn more about push back racking systems, contact a material handling professional at Raymond West today. Our storage design experts can help you find a solution that is ideal for your application.
Raymond West's Stockton facility serves much of the northern Central Valley, including Stockton, Lathrop, Lodi, Tracy, Modesto, and Merced.
Raymond West | Stockton Material Handling Equipment Supplier
19107 Christopher Way
Lathrop, CA 95330
(800) 675-2500