Implementing a Shuttle System In Your Warehouse
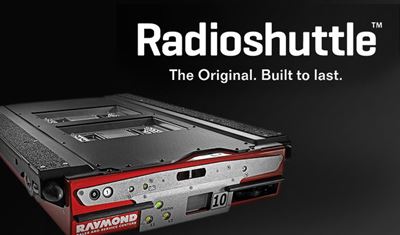
Why add a pallet shuttle system to your warehouse? Find out about the features and benefits of Raymond's Radioshuttle.
The New Reality of Warehousing
All over the West, warehouse prices are skyrocketing. Between a booming economy and an explosion in e-com operations, storage and distribution real estate is at an all-time premium. Prices will continue to rise, meaning that warehouse operators will need to adapt to this new reality in warehouse costs.
Smart operators are maximizing their warehouse utilization with tighter aisles, denser racking configurations and automation solutions. Using one, two or all three of these strategies will not only expand the capacity of your existing warehouse footprint, but also improve productivity and reduce labor expenses in the process.
Pallet Shuttles
One of the simplest and most effective high density racking and automation solutions is the utilization of pallet shuttles. These are radio controlled shuttles that travel the depth or your racking, picking up and depositing pallets at the face of either end of the racking structure.
With this type of configuration, you can increase your racking depth exponentially, start to eliminate aisles and even increase the height of your racking structure, maximizing the utilization of your cubic footage.
Of course pallet shuttle systems are not a panacea for all storage problems. Deep racking systems mean that your selectivity is not as flexible as standard selective rack. However, for operations with high throughput and lower SKU counts, shuttle configurations are often a perfect solution.
Flexible Configuration
These types of systems can also be set up with a dynamic pallet flow case pick tunnel at the base level of the racking system. Replenishment pallets are stored at upper levels to feed pallet flow pick lanes at lower levels. All case picking takes place from within a picking tunnel that passes through the rack at ground level.
The buffer pallets are handled by lift trucks and the shuttles in a separate truck corridor that is perpendicular to the pick tunnel. This is an extremely efficient and space saving way of storing pallets in the immediate picking area, while maintaining a safe and efficient pick aisle.
Even greater flexibility can be achieved with a combination of a mezzanine and pallet shuttle system. An open area for product staging is created at ground level with all buffer storage in columns above. This type of configuration is a winning combination of selectivity and storage density
Pallet runners allow either last in first out (LIFO) or first in first out (FIFO) configurations, depending on whether you keep the rack faces accessible on one end or both. FIFO configurations are ideal for applications like grocery or other perishable item management while LIFO can be used for accumulation and disbursement types of scenarios.
Talk To An Expert
If you’d like to learn more about Raymond’s Radioshuttle option, or other ways to increase your warehouse density and productivity through automation, talk to a Raymond West expert.