Defining AS/RS Technologies: Bin and Tote Systems
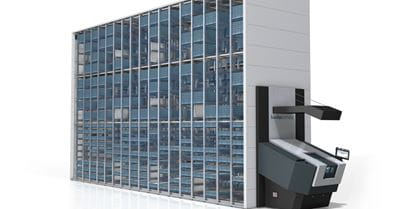
In contrast to shelf based picking systems, bin based systems deliver a bin or tote of products to the operator as opposed to an entire shelf or tray.
Material handling operations all over the world have been forever changed by e-commerce. With the emphasis shifting away from picking pallets and cases and toward picking individual items or "eaches," there has been an explosion of AS/RS technologies on the market to assist warehouse, distribution, and manufacturing operations in making this transition.
There are three main categories of goods-to-person AS/RS systems, including robotic, shelf based and bin/tote based picking systems. In contrast to shelf based picking systems, bin based systems deliver a bin or tote of products to the operator as opposed to an entire shelf or tray. There are two main categories of bin and tote based systems.
Crane-Based Mini-Load AS/RS
Mini load systems are capable of handling a wide range of loads. Mini-loads handle products in cases, totes, or trays with a single crane-mounted load handling device dedicated to each extremely dense rack aisle. The cranes deliver product to the operator via a workstation at the end of the aisle, either on rails or wheels, at high very high speeds.
In a mini-load system, the racks can be configured for single or double deep storage. In a single deep location, the average weight is around 100 pounds, and in a double deep location, it's around 200 pounds. Mini-loads, which are ideal for lower turnover items, can deliver 1 load per minute, with throughput rates of 60 to 100 lines per hour. This is an ideal high-density storage solution if you have more than 10,000 totes or 25,000 SKUs to store.
Vertical Buffer Modules (VBMs)
A vertical buffer module is a bin handling system meant for smaller applications (fewer than 10,000 totes or 25,000 SKUs) where a larger, more expensive system can’t be cost justified. A Vertical Buffer Module is an enclosed shelving system with a movable mast running down a center aisle for storage and picking of totes. For maximum system throughput, the unit is programmed to work ahead of the operator and queue the next pick as the current pick is handled.
Totes can be handled automatically with an inbound and outbound conveyor or passed to an ergonomic turntable picking station. A manual station can be added to the machine to allow for tote replenishment during picking operations. Picking does not need to be paused while replenishment occurs.
Totes can be delivered to remote picking stations and multiple units can be connected via conveyor. These systems are scalable, modular, and very energy efficient.
Learn More About AS/RS
To get more information on available AS/RS options, speak with an automation expert at Raymond West today!