Reducing Downtime with Predictive Forklift Maintenance: How Raymond’s iTrack System Can Help
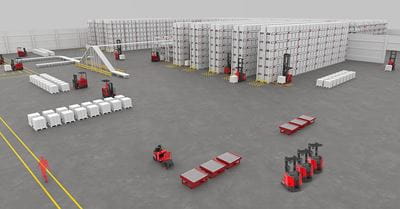
Predictive forklift maintenance can significantly reduce downtime and costs in warehouses. Raymond’s iTrack system leverages real-time data and analytics to anticipate maintenance needs, streamline repairs, and optimize fleet performance for improved efficiency and reliability.
In the fast-paced world of warehousing and logistics, forklift downtime isn’t just an inconvenience—it’s a costly disruption. Every minute a forklift is out of commission translates to delayed shipments, idle workers, and lost revenue. Traditional reactive maintenance strategies—waiting for something to break before fixing it—often lead to unexpected failures, emergency repairs, and escalating costs. Enter predictive forklift maintenance—a proactive approach that leverages real-time data, analytics, and technology to anticipate issues before they become critical. One of the most effective tools for implementing predictive maintenance is Raymond’s iTrack Asset and Maintenance Management System. By providing unparalleled visibility into maintenance costs and fleet performance, iTrack empowers warehouse managers to optimize operations, reduce downtime, and control expenses. Downtime isn’t just about a single forklift sitting idle. It creates a domino effect: Operational Disruptions: Without a fully functional fleet, productivity slows, leading to missed deadlines and order backlogs. Labor Inefficiencies: Workers may be forced to share equipment, leading to bottlenecks and reduced throughput. Emergency Repair Costs: Unplanned repairs are often more expensive than scheduled maintenance, with additional costs for rush service and expedited parts. Shortened Equipment Lifespan: Frequent breakdowns accelerate wear and tear, reducing the longevity of forklifts and increasing capital expenditures. A predictive maintenance strategy—powered by data-driven insights from Raymond’s iTrack system—addresses these challenges head-on. Predictive maintenance is not guesswork—it’s a science. It relies on real-time monitoring, historical data, and advanced analytics to detect potential failures before they happen. Here’s how it works: Continuous Monitoring: Sensors and software track forklift usage, battery health, operating hours, and maintenance history. Data Analysis: The system identifies trends, such as recurring breakdowns or excessive wear on specific components. Proactive Alerts: When potential issues are detected, automated notifications prompt maintenance teams to address them before they escalate. Optimized Scheduling: Maintenance tasks are scheduled at the most convenient times, minimizing disruptions to daily operations. Raymond’s iTrack system plays a crucial role in executing this strategy efficiently. Do you know which forklifts in your fleet are costing you the most in repairs? 🔹 Key Feature: Cost/utilization matrix—quickly determine if an asset should be reallocated, replaced, or repaired. Instead of reacting to breakdowns, iTrack allows managers to schedule maintenance before a failure occurs. This ensures that small issues—like a worn-out tire or declining battery efficiency—are addressed before they escalate into major problems. 🔹 Key Feature: Automated maintenance reports—stay ahead of wear and tear with customized alerts and service reminders. Managing invoices from multiple service providers can be a logistical nightmare. iTrack consolidates all invoices into a single, electronic document, reducing processing time and administrative costs. 🔹 Key Feature: Customizable invoices—break down costs by site, truck type, or purchase order for easy reconciliation. When a repair is needed, time is of the essence. iTrack’s dispatch module allows warehouse managers to request service remotely, track technician activity, and monitor repair times—ensuring that forklifts are back in operation as quickly as possible. 🔹 Key Feature: Dispatch KPI tracker—evaluate service provider performance for better accountability and faster resolutions. Keeping track of maintenance costs across an entire fleet can be overwhelming. iTrack provides at-a-glance expense summaries, helping managers stay within budget and justify maintenance investments. 🔹 Key Feature: Interactive reporting—drill down from enterprise-wide data to individual forklifts with a few clicks. Raymond’s iTrack system is not just a maintenance tool—it’s part of a broader effort to optimize fleet efficiency and reduce operational costs. When combined with Raymond’s iWAREHOUSE® telematics system, businesses gain even deeper insights into operator performance, impact detection, and fleet utilization. Together, these tools create a data-driven ecosystem where: In today’s competitive warehouse environment, downtime is not an option. Raymond’s iTrack system transforms forklift maintenance from a reactive process into a proactive strategy, helping businesses: ✔ Reduce unexpected breakdowns and costly emergency repairs. By leveraging real-time insights and predictive analytics, warehouses can maximize uptime, improve efficiency, and save money—all while maintaining a safer and more productive work environment. The question is no longer whether you can afford predictive maintenance. It’s whether you can afford not to use it.
The High Cost of Forklift Downtime
How Predictive Maintenance Works
How Raymond’s iTrack System Reduces Downtime
1. Unmatched Visibility into Fleet Health
With iTrack’s web-based platform, managers can monitor maintenance trends, identify high-cost assets, and make data-driven decisions about fleet allocation, repairs, and replacements.2. Proactive Maintenance Scheduling
3. Reduced Administrative Burden with Single-Source Invoicing
4. Faster Service Response Times
5. Real-Time Expense Tracking
The Bigger Picture: iTrack as Part of a Comprehensive Fleet Management Strategy
✅ Forklifts are maintained proactively rather than reactively.
✅ Maintenance costs are predictable and controlled.
✅ Operations experience less downtime and fewer disruptions.
Conclusion: A Smarter Approach to Forklift Maintenance
✔ Extend the lifespan of their equipment with smarter maintenance scheduling.
✔ Lower administrative costs through single-source invoicing.
✔ Gain full visibility into fleet performance and maintenance expenses.