Failure of Forklift Load Wheels
Tracking the Life of Your Load Wheels
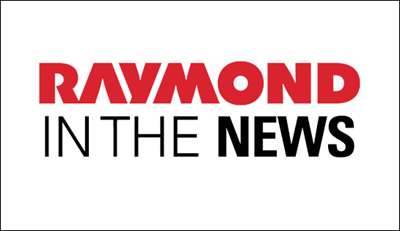
Save money and decrease downtime by tracking the life of your load wheels.
Here are some ways to prevent failure of your load wheels.
- Extend the life of your load wheels by choosing the right durometer for your application. The durometer is the hardness of the load wheel’s compound based on a 0-100 scale. The higher the durometer, the harder the compound. The average durometer for a forklift load wheel will range from 80-97. A lower durometer of around 85 will give your forklift operator, a smoother, more absorbent ride. A higher durometer may give your load wheels a longer life. It is important to take warehouse conditions in to consideration.
- Damaged floors will shorten the life of your load wheels. Cracks, potholes, bumps and uneven floors all can cause serious damage to both your load wheels and your forklift. The hard hits and brunt force can cause the cracking and chunking of the load wheel.
- Dirty floors also play a part in shortening the life of your load wheels. Cracking and chunking may be a result of debris being caught between the load wheels.
- Dragging a pallet across the floor will have a tremendous effect on your load wheels. Most operators are required to be highly efficient when loading and unloading trucks. They may try to save time by pushing pallets across the floor. This will cause intense heat to the load wheels that can result in the wheels delaminating (compound comes off the hub). All employees should be trained on the proper use of warehouse equipment.
Note: The color of the load wheel is not an indication of its durometer. To find out the durometer of your load wheels, contact your local Raymond West Sales representative. They can test a wheel’s durometer and make recommendations of the correct durometer for your application.