Warehouse Automation | Portland, OR
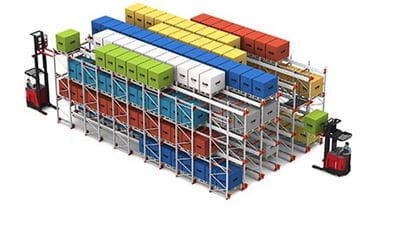
Warehouse costs are skyrocketing. Smart warehouse operators are squeezing every last dollar out of their facilities though increased density and automation technology.
Raymond West is the premiere warehouse automation supplier in the Pacific Northwest. To speak with an automation expert, give us a call today at (800) 675-2500.
In markets like the Western United States, warehouse space is at a record setting premium. Online E-com operations have greatly reduced warehouse inventory and as a result, leasing costs throughout the region have skyrocketed year after year.
As facility costs climb, it’s imperative to make sure that you’re using space as efficiently as possible. For smart warehouse operations, that means maximizing density and automating everything that can be mechanized.
Fortunately, cutting edge material handling technology has evolved swiftly in the last few years, giving you the tools you need to increase your density and efficiency at unprecedented levels. Storage tech is swiftly altering the elemental concepts of warehouse storage solutions.
Warehouse Automation
Automated storage and retrieval systems (AS/RS) are an economical force of nature in the warehouse. Here’s a list of the main reasons for implementing AS/RS systems:
- Monumental leaps in efficiency. AS/RS systems reduce employee costs, liberate floor space, diminish inadvertent inventory breakage, and increase throughput.
- Greater stocking ability. Gains in efficiency mean that enterprises have the ability to increase the number of SKUs and increase the volume of existing operations for better financial performance.
- Lift truck operating cost reductions. An automated warehouse system slashes forklift hours and distance traveled.
- Enhanced Coordination. Automated solutions enable complex sequencing and buffering possibilities that can be coordinated with loading hours and route options.
- Quality control. AS/RS systems are incredibly precise and are a better choice for handling detail oriented duties than human resources.
- Enhanced safety. Less human intervention connotes fewer safety incidents.
- Adaptability. When it comes to order aggregation, assembly/enrichment, storage, put-away and replenishment, AS/RS systems are increasingly flexible solutions that can automate almost any warehouse process.
Automated Storage and Retrieval System
Just what exactly is AS/RS? There are various technologies that are classified as AS/RS systems, including the following:
- Vertical lift modules
- Horizontal carousels
- Vertical carousels
- Fixed aisle systems
Vertical Lift Modules
Like a vertical carousel, vertical lifts are vertically aligned systems that store trays in an upright metal column. In contrast to a carousel, a VLM has an extractor system that moves upward and downward inside the module, retrieves specific bins and delivers them directly to the user.
Horizontal Carousels
Horizontal carousels are similar in concept to that automatic rack your drycleaner uses to fetch your clothes. They are generally used for small products and they are an array of receptacles suspended from a rasied rail. Many times they are coupled with voice picking systems or pick-to-light systems.
Vertical Carousels
Vertical carousels are vertically driven, and are somewhat like a Ferris wheel with storage platforms fastened to a circular drive system that spins on a perpendicular horizontal axis. They are usually housed in an upright metal casing.
Fixed Aisle AS/RS
Fixed aisle systems are generally configured as two columns of racking with a narrow channel separating the two. In the center of the aisle is a raised metal track with a vertical mast that maneuvers its length. Connected to the upright is a vertically traveling carrier fitted with a load handling mechanism.
This upright and carriage is known as as the SRM (storage and retrieval machine) or crane. The majority of systems use a single SRM per aisle, but more advanced systems may have more than one.
Categorically, there are a couple of types of fixed aisle systems. Unit-load systems are designed to deal with bigger loads on pallets. Mini-load systems (oftentimes called a case-handling system or tote stacker) are lightweight installations that can deal with cartons and smaller items.
Warehouse Automation Systems Near Me
Talk to an expert! If you’d like support in evaluating warehouse automation options for your material handling operation, contact a technical expert at Raymond West.
Our engineering group will work with you to assess on-site equipment design for your warehouse or distribution center. We will help you develop a business case including conditions, process, future requirements, training and total cost.
We provide service and support from our locations throughout the West. Whether you need new or used equipment, maintenance, parts, service or training, we offer a comprehensive array of material handling services and products.
Raymond's Portland service operation includes all of Western Oregon and Southwest Washington, including Portland, Beaverton, Tigard, Hillsboro, Forest Grove, Sherwood, Tualatin, Wilsonville, Oregon City, Gladstone, Clackamas, Milwaukie, Happy Valley, Gresham, Troutdale, Woodburn, Salem, Vancouver, Ridgefield, Longview, Kelso and surrounding areas.
Raymond West | Portland Material Handling Equipment Supplier
3148 NE 181st Ave
Portland, OR 97230
(800) 675-2500