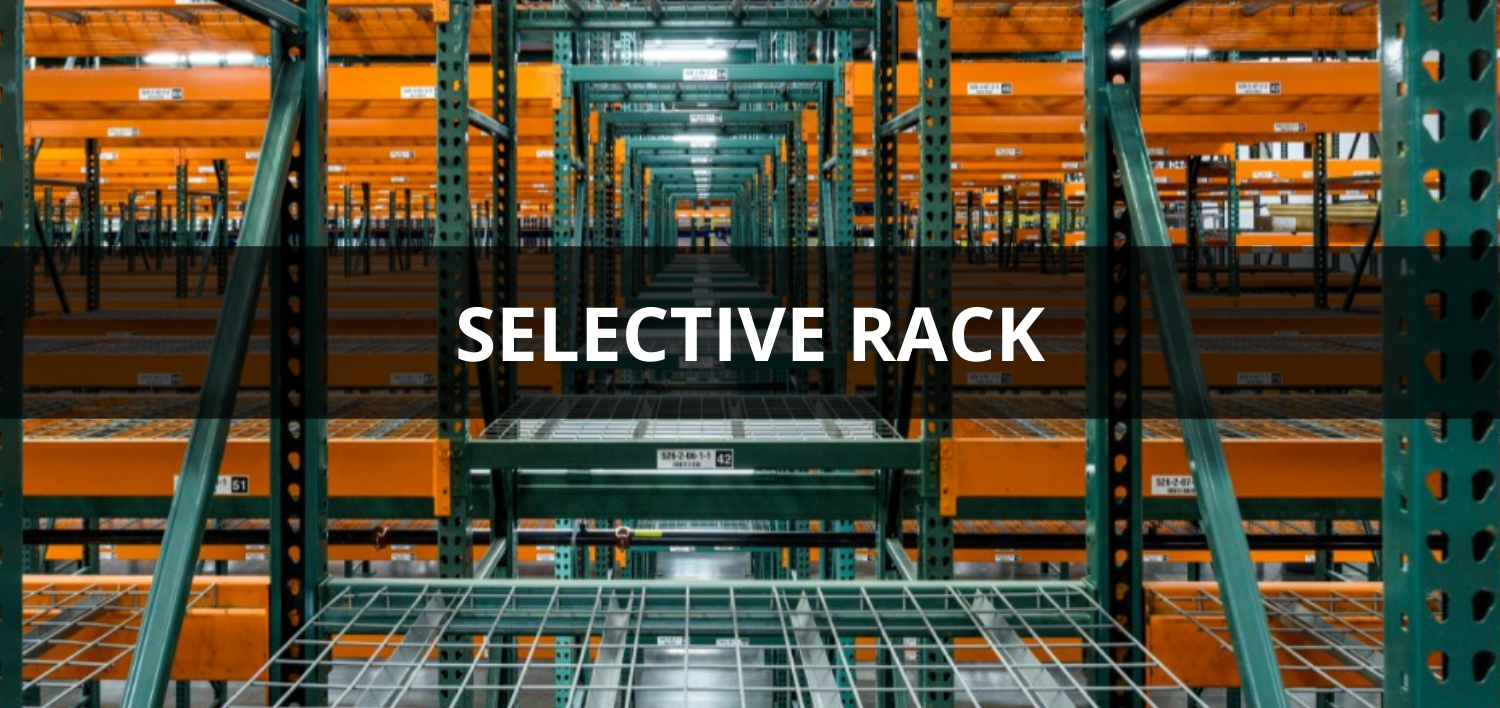
-
Selective Rack Is the most common pallet racking system used today. It uses the First-In-First-Out (FIFO) method and allows for immediate retrieval of inventory. Each bay is constructed by the combination of vertical upright frames and horizontal load beams and comes in different configurations, capacities and sizes. Typically, there are two types of configurations: roll formed, or clip-in configuration, and a structural bolt-together configuration. Layout options include single deep, double deep and back-to-back.
- Roll formed selective rack is most commonly manufactured in a “teardrop “style. Pallets then rest on the horizontal load beams that are held in place by mounting clips. Because the clips on teardrop configurations can be quickly moved, the shelves can be easily adjusted to different heights to accommodate various load sizes. This is convenient for a warehouse that needs to store a wide variety of product sizes.
- Structural pallet rack systems are very similar to roll formed pallet rack systems except the horizontal load beams are attached to the uprights with bolts and have much greater weight-bearing capacity. The bolt fixings make this a form of adjustable shelving - racks can be constructed, reconfigured, and dismantled and reused as necessary.
Very Narrow Aisle, otherwise known as VNA, is the use of selective pallet racking in a tighter configuration to provide maximum space utilization within a storage facility. These systems typically operate in conjunction with wire-guided or rail-guided reach-truck systems. A wire-guided system consists of a wire embedded in the concrete floor that provides tracking for the reach-truck. A distinct advantage of a narrow aisle pallet racking is fast picking without large aisles which results in improved use of space. When there is limited space, a compact storage method is ideal.
Raymond Trucks Compatible With Selective Rack Systems
Selective Pallet Rack systems can save you money by providing the most efficient use of space for your warehouse, while increasing versatility and efficiency.