Warehouse Automation
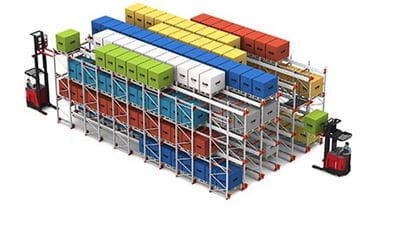
Warehouse costs are skyrocketing. Smart warehouse operators are squeezing every last dollar out of their facilities though increased density and automation technology.
Raymond West is the premiere warehouse automation supplier in the San Fernando Valley. To speak with an automation expert, give us a call today at 661-206-0462.
In Southern California, warehouse space is fetching a record setting premium. Online E-com operations have put tremendous pressure on inventory and as a result, rental contract costs in many areas have gone through the roof year after year, especially in Los Angeles, Orange County and the Inland Empire.
As facility costs rise, it's vital to make sure that you're using space in the most efficient manner possible. For savvy warehouse operations, that means maximizing density and automating processes wherever possible.
Luckily, high performance material handling technology has evolved rapidly in recent years, allowing you the opportunity to increase your efficiency and density like never before. Storage tech is quickly altering the elemental concepts of warehouse storage solutions.
Warehouse Automation
Automated storage and retrieval systems (AS/RS) are an economical force of nature in the warehouse. A few of the top reasons for investing in AS/RS systems:
- Huge efficiency increases. AS/RS systems cut employee costs, recover floor space, lessen unintended inventory damage, and increase productivity.
- Greater stocking ability. Efficiency gains mean that enterprises have the ability to increase the number of SKUs and increase the output of their operations for better financial performance.
- Lift truck operating cost reductions. An automated warehouse system slashes forklift travel distance and hours.
- Advanced Facilitation. Automated solutions provide compound sequencing and buffering alternatives that can be coordinated with shipping times and route options.
- Quality control. AS/RS systems are extremely reliable and are better at handling complex tasks than human resources.
- Improved safety. Reduced reliance on humans connotes fewer safety incidents.
- Versatility. When it comes to order aggregation, assembly/enrichment, storage, replenishment and put-away, AS/RS systems are becoming more and more versatile.
Automated Storage and Retrieval System
What is AS/RS? There are several types of technologies that are classified as AS/RS systems, including these:
- Vertical lift modules
- Horizontal carousels
- Vertical carousels
- Fixed aisle systems
Vertical Lift Modules
Akin to a vertical carousel, VLMs are vertically positioned systems that hold trays in a tall metal casing. However, a VLM has a puller system that moves upward and downward inside the module, retrieves individual bins and presents them to the operator.
Horizontal Carousels
Horizontal carousels are in some ways like that automatic rack your dry cleaner uses to store and retrieve your clothing items. They're generally employed for smaller sized products and they are a succession of receptacles suspended from a raised track. Quite often they will be integrated with voice picking systems or pick-to-light systems.
Vertical Carousels
As one would expect, vertical carousels are vertically aligned, and are a bit like a Ferris wheel with storage platforms attached to a circular drive system that spins on a perpendicular horizontal axis. Vertical carousels are generally contained in an upright metal casing.
Fixed Aisle AS/RS
Fixed aisle systems are generally configured as two columns of racking with a narrow channel separating the two. In the center of the aisle is an elevated metal rail with an upright mast that travels along it. Connected to the mast is a vertically traveling carriage fitted with a load handling device.
This upright and carriage is known as the crane or SRM. The majority of systems use one SRM per aisle, but more specialized systems may have more than one.
Categorically, there are two varieties of fixed aisle systems. Unit-load systems are designed to manage bigger loads on pallets. Mini-load systems (often known as a case-handling system or tote stacker) are smaller installations that can deal with cartons and smaller goods.
Warehouse Solutions
Talk to an expert! If you need assistance in assessing warehouse automation options for your Southern California material handling operation, contact a technical expert at Raymond West by calling 661-206-0462.
Our technical team will work with you to assess on-site equipment design for your warehouse or distribution center. We'll help you build a business case including process, conditions, future requirements, training and total cost.
We provide service and support from our locations throughout California, Nevada and Arizona. Whether you need new or used equipment, maintenance, parts, service or training, we provide a comprehensive selection of material handling services and products.