Warehouse Automation | Boise
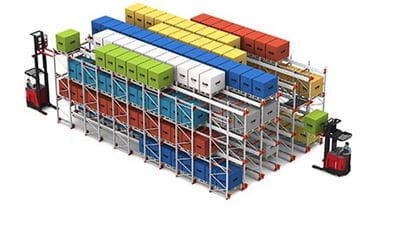
Warehouse costs are skyrocketing. Smart warehouse operators are squeezing every last dollar out of their facilities though increased density and automation technology.
Raymond West is the premiere warehouse automation supplier in the Treasure Valley. To speak with an automation expert, give us a call today at (800) 675-2500.
Across the West, warehouse space is priced at an all-time premium. Online E-com operations have put tremendous pressure on inventory and as a result, leasing costs in many areas have risen by double digits in recent years, especially in the Northwest.
As storage costs climb, it's imperative to make sure that you're using your facility space in the most efficient manner possible. For smart warehouse managers, that means increasing density and automating everything that can be mechanized.
Luckily, high performance material handling technology has evolved swiftly over the last several years, giving you the ability to increase your density and efficiency at unprecedented levels. Automation technology is swiftly altering the very nature of warehouse storage solutions.
Warehouse Automation
Automated storage and retrieval systems (AS/RS) are an economical force of nature in the warehouse. Some of the top reasons for adding AS/RS systems:
- Huge efficiency increases. AS/RS systems cut employee costs, recover floor space, reduce unintended inventory destruction, and increase productivity.
- Increased Capacity. Becoming more efficient means that enterprises can increase the number of SKUs and increase the volume of existing operations for better financial performance.
- Lift truck operating cost reductions. An automated warehouse system cuts forklift hours and distance traveled.
- Enhanced Facilitation. Automated solutions enable compound buffering and sequencing possibilities that can be coordinated with freight hours and route options.
- Quality oversight. AS/RS systems are simply more accurate and are a better choice for handling detail oriented tasks than humans.
- Enhanced safety. Reduced reliance on humans means fewer safety mishaps.
- Adaptability. When it comes to order consolidation, value adds, storage, put-away and replenishment, AS/RS systems are transforming into increasingly adaptable tools.
Automated Storage and Retrieval System
So what exactly is AS/RS? There are many different technologies that are classified as AS/RS systems, including these:
- Vertical lift modules
- Horizontal carousels
- Vertical carousels
- Fixed aisle systems
Vertical Lift Modules
Similar to a vertical carousel, VLMs are vertically aligned systems that store trays in an upright metal column. In contrast to a carousel, a VLM has a retriever system that travels vertically within the column, retrieves specific bins and delivers them to the operator.
Horizontal Carousels
Horizontal carousels are similar in concept to that rack your drycleaner uses to store and retrieve your clothing items. They're typically used for less bulky products and they are a series of receptacles suspended from an upper track. Quite often they will be coupled with voice picking systems or pick-to-light systems.
Vertical Carousels
As one would expect, vertical carousels are vertically aligned, and are somewhat like a Ferris wheel with storage platforms attached to a revolving system that travels in an up and down motion. They are generally concealed in an upright metal column.
Fixed Aisle AS/RS
Fixed aisle systems are typically designed with two rows of racking with a narrow channel separating the two. The center of the aisle has an elevated steel track with a tall mast that travels along it. Attached to the upright is a vertically maneuvering carriage outfitted with a load handling device.
This upright and carrier device is referred to as the SRM (storage and retrieval machine) or crane. Most systems use a single SRM per corridor, but more sophisticated systems may have more than one.
Categorically, there are two classifications of fixed aisle systems. Unit-load systems are designed to manage larger loads on pallets. Mini-load systems (often referred to as a case-handling machine or tote stacker) are lightweight installations that can handle cartons and smaller products.
Warehouse Solutions
Talk to an expert! If you need advice in assessing warehouse automation options for your Idaho material handling operation, contact a specialist at Raymond West by calling (800) 675-2500.
Our technical group will work with you to assess on-site equipment design for your warehouse or distribution center. We will help you build a business case including process, conditions, training, future needs, and total cost.
We provide service and support from our locations throughout the Western United States. Whether you need new or used equipment, maintenance, parts, service or training, we supply a comprehensive range of material handling services and products.
Raymond West's Boise service center serves most of Idaho, including Boise, Nampa, Meridian, Idaho Falls, Caldwell, Pocatello, Twin Falls, Post Falls and surrounding areas.
Raymond West | Boise Material Handling Equipment Supplier
743 W McGregor Ct #100
Boise, ID 83705
(800) 675-2500