Warehouse Automation
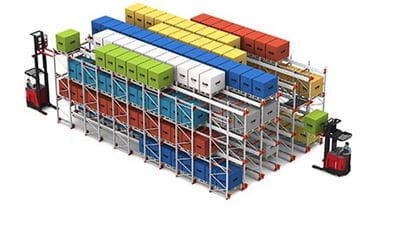
Warehouse costs are skyrocketing. Smart warehouse operators are squeezing every last dollar out of their facilities though increased density and automation technology.
Raymond West Inc is the premiere warehouse automation supplier in Metro Phoenix. To speak with an automation expert, give us a call today at (602) 275-2228.
Across the West, warehouse space is priced at a record setting premium. Online E-com operations have put tremendous pressure on inventory and as a result, rental costs throughout the region have increased substantially year after year, particularly in larger metropolitan areas.
As facility costs rise, it's crucial to ensure that you're employing warehouse space in the most efficient manner possible. For smart warehouse operations, that means maximizing density and automating as much as possible.
Fortunately, high performance material handling technology has advanced swiftly in the last few years, giving you the tools you need to increase your density and efficiency by extraordinary margins. Storage tech is quickly altering the elemental concepts of warehouse storage solutions.
Warehouse Automation
Automated storage and retrieval systems (AS/RS) are a game changer in the warehouse. Some of the primary reasons for implementing AS/RS systems:
- Massive increases in efficiency. AS/RS systems slash labor costs, save floor space, reduce unintended inventory destruction, and increase productivity.
- More products. Efficiency gains mean that businesses have the ability to increase the number of SKUs and increase the output of existing operations for an improved bottom line.
- Lift truck cost savings. An automated warehouse system cuts forklift travel distance and hours.
- Advanced Facilitation. Automated solutions enable intricate buffering and sequencing possibilities that can be synchronized with freight times and route options.
- Quality oversight. AS/RS systems are incredibly precise and are more suitable for handling detail oriented functions than human resources.
- Enhanced safety. Reduced reliance on humans means fewer safety mishaps.
- Versatility. When it comes to order aggregation, value adds, storage, replenishment and put-away, AS/RS systems are increasingly flexible solutions that can automate almost any warehouse process.
Automated Storage and Retrieval System
Just what exactly is AS/RS? There are various technologies that are considered to be AS/RS systems, including these:
- Vertical lift modules
- Horizontal carousels
- Vertical carousels
- Fixed aisle systems
Vertical Lift Modules
Like a vertical carousel, VLMs are vertically positioned systems that maintain receptacles in a tall metal casing. Unlike a carousel, a VLM has an extractor mechanism that advances up and down in the center of the module, retrieves discrete trays and hands them to the operator.
Horizontal Carousels
Horizontal carousels are kind of like that automatic rack your drycleaner uses to store and retrieve your garments. They're generally employed for small products and they are a series of receptacles mounted on a rasied track. Many times they are paired with voice picking systems or pick-to-light systems.
Vertical Carousels
As the name suggests, vertical carousels are vertically driven, and are somewhat like a Ferris wheel with storage platforms attached to a revolving system that goes from top to bottom. Vertical carousels are typically contained in a tall metal casing.
Fixed Aisle AS/RS
Fixed aisle systems are usually set up as two columns of racking with a narrow corridor separating the two. The center of the aisle has a raised metal track with a vertical mast that maneuvers its length. Connected to the mast is a vertically maneuvering carrier fitted with a load handling apparatus.
This upright and carrier device is known as the crane or SRM. The majority of systems use a single SRM per aisle, but more advanced systems may have multiple.
In general, there are two varieties of fixed aisle systems. Unit-load systems are designed to deal with bigger loads on pallets. Mini-load systems (often referred to as a case-handling system or tote stacker) are lightweight implementations that can handle cartons and smaller goods.
Warehouse Solutions
Talk to an expert! If you 'd like assistance in assessing warehouse automation options for your Southern California material handling operation, contact a professional at Raymond West Inc by calling (602) 275-2228.
Our engineering group will work with you to evaluate on-site equipment design for your warehouse or distribution center. We'll help you develop a business case including process, conditions, training, future needs, and overall cost.
We provide service and support from our locations throughout California, Nevada and Arizona. Whether you need new or used equipment, maintenance, parts, service or training, we supply a full range of material handling products and services.
You May Also Like:
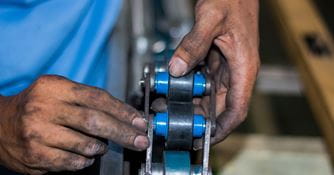
Conveyor Repair | Phoenix
Raymond West is a Phoenix warehouse automation equipment supplier. We offer repair and service for many types of conveyor systems. Call us today at (602) 275-2228.
Learn More
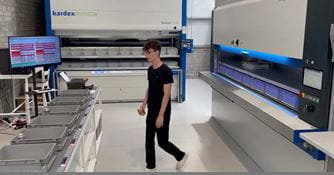
Pick To Light Solutions |Phoenix
Pick to light systems are efficient, high throughput systems that can transform your warehouse and increase profitability.
Learn More
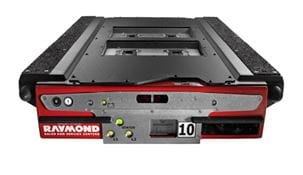
Pallet Shuttles
We supply a full range of warehouse automation equipment including pallet shuttle systems. If you'd like to find out more about automation possibilities for your warehouse, give us a call today.
Learn More
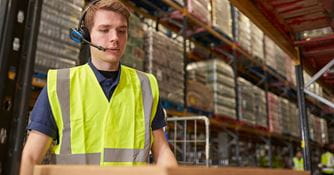
Order Picking Systems | Phoenix
We design, install and maintain state-of-the-art order picking solutions for all types of warehouse and distribution center operators.
Learn More